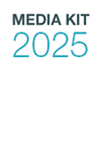
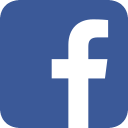
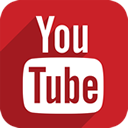
Yanfeng China selects ELIX Polymers’ PC/ABS for interior parts
Zespri launches home compostable label for kiwifruit
Syensqo launches flame retardant PPA for critical EV components
EREMA to show new PredictOn solution at K 2025
Pre K | DOMO Chemicals to show specialized solutions for a low-carbon future
Pre K | Covestro unveils its focuses at K 2025
Round Table at Fakuma 2023: “Plastic – Recyclable Rather Than Problem Material!”
ArabPlast 2023 – The Success Journey Continues………..
GREAT NEWS! INAPA 2023 IS COMING BACK 24 - 26 May 2023 at JIExpo Jakarta, Indonesia
ASEAN: The Next Manufacturing Hub
Innovative and Sustainable Packaging
Green Plastics: News & Insights
KRAIBURG TPE Boosts Smart Skin Diagnostic Device Probe Protector with Innovative TPE Solutions
Pre K | Innovative silicone solutions from WACKER
Pre K | Envalior advanced TPC for shoe midsoles
[Webinar playback] WANHUA: High-performance Specialty Plastics Enable High-quality Industrial and Life Applications
【Mandarin session:Webinar playback】Covestro: RE Material Solutions: Empowering electronics industry to fulfill new EPEAT standards and lower carbon footpint
【Mandarin session:Webinar playback】Covestro: Covestro's CMF Trends 2025+: Electronics, Automotive and Healthcare
Jiangsu Liside New Material Co., Ltd.
Dow 45 years in China
Carbon Removal and Carbon Emission Reduction Tech Solution——Yuanchu Technology (Beijing) Co. Ltd.
Playback TECHHUB 2025@CPRJ Live Streaming for CHINAPLAS
Playback TECHHUB@CPRJ Live Streaming for CHINAPLAS
Playback On April 14, the "6th Edition CHINAPLAS x CPRJ Plastics Recycling and Circular Economy Conference and Showcase" at the Crowne Plaza Shenzhen Nanshan is currently being livestreamed!
Playback 5th Edition CHINAPLAS x CPRJ Plastics Recycling and Circular Economy Conference and Showcase
1. Variable die temperature quenching and quenching technology is used to shorten the forming cycle of optical products 2. Recycling of materials that have never been used before in the field of optical molding 3. Show a new optical field to reduce production cost solutions
Speakers
YAN WENJUN
Shanghai Matsui Machinery Co., LTD |Consulting manager
Ask a question
He majored in thermophysics at the School of Thermal Engineering, National Institute of Technology, Japan. He then joined Matsui Manufacturing Co., LTD., which has a history of 111 years, and engaged in specialized research. Matsui is well known in the industry for developing and manufacturing professional equipment for plastic forming and processing. In recent years, Matsui has taken improving the resource productivity of plastic molding plants as a topic to help plastic molding plants achieve true green production, so that they can use half of the resources to create double capacity, so as to achieve four times the wealth value. The proposal to reduce the cost of optical molding brought to you this time is also starting from this perspective. My professionalism enables me to subconsciously find potential problems and devote myself to exploring added value when I participate in the research and development and exploration of this project.
Host Introduction
Founded in 1912, Matsui Co., Ltd. specializes in the development and manufacture of auxiliary machinery around plastic forming.
As a global multinational company, Matsui has established more than 90 locations in 26 countries and regions around the world.
Shanghai Matsui Machinery Co., LTD., located in Xinzhuang Industrial Zone, Shanghai, is a subsidiary of Shanghai Matsui Machinery Co., Ltd. established in 1997, and has set up 13 locations.
Faced with a large number of "energy waste", "resin waste" and "water waste" in molding factories, Matsui proposed the factor4 environmental protection concept of "creating double wealth with half resources". From the three directions of [production UP] [added value UP] [resource consumption CUT], divided into 12 topics, more than 200 kinds of green molding schemes were launched.